Overview
Quality at Every Step, from Every Team
At Grid Automation, our quality culture is built on providing exceptional experiences to our customers through every interaction with our people and products. Quality is core to our DNA, our policies, and procedures. We start by listening intently to our customers, understanding their current and future requirements, and applying learnings to future innovation with humility and integrity.
We believe and support 3 pillars to quality: people, process, and routine validation.
Empowering our People
Our people are the ambassadors of our brand. We actively invest in the right training curriculum and process support tools for our teams. Ongoing mentorship allows employees to grow and develop the skills necessary to drive a “receive no defect, create no defect, ship no defect” culture. Our employees are accountable to our customers and are empowered to stop the line whenever they have concerns about quality.
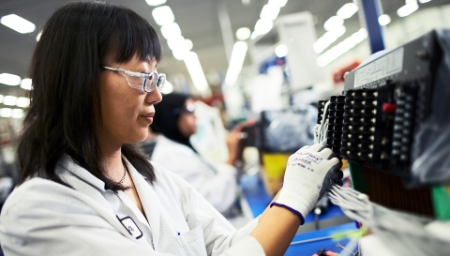
Our people are the ambassadors of our brand. We actively invest in the right training curriculum and process support tools for our teams. Ongoing mentorship allows employees to grow and develop the skills necessary to drive a “receive no defect, create no defect, ship no defect” culture. Our employees are accountable to our customers and are empowered to stop the line whenever they have concerns about quality.
Robust Processes
We ensure compliance with laws and regulations pertaining to the quality, safety, and performance requirements in the countries in which Grid Automation products and services are offered. Our well-established, repeatable processes are driven by lean and six-sigma principles. In addition, we perform rigorous surveillance and re-registration audits through internal and external registrars. We are proud to hold:
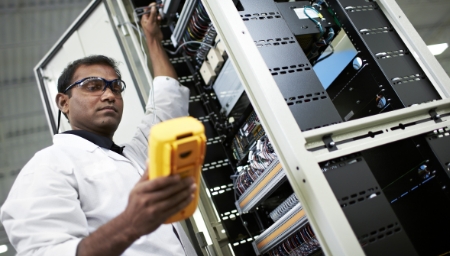
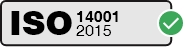
ISO14001:2015
Environmental Management Systems
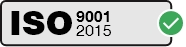
ISO9001:2015
Quality Management Systems
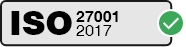
ISO 27001 - 2017
Information Security Management System * Not applicable to all Grid Automation sites
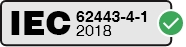
IEC62443-4-1:2018
Security for Industrial Automation and Control Systems Part 4-1: Product Security Development Life-Cycle Requirements
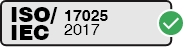
ISO/IEC 17025 2017
Testing and calibration laboratories * This certification applicable only to labs in Stafford, UK and Markham, Canada
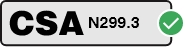
CSA N299.3
Supply of items and services for nuclear power plants, Category 3 * Applicable only to relays and panels built in Markham, Canada
Data Driven Decisions
We set the bar high and measure success at each step of our product lifecycle whether it's design validation, supplier qualification, manufacturing measurements or customer satisfaction. Continuous improvement initiatives are data driven, using eight disciplines of problem solving (8D) and 5-Why methodologies.
Our people, processes, and state-of-the art systems work together to ensure we deliver on our quality promise for customers around the world.
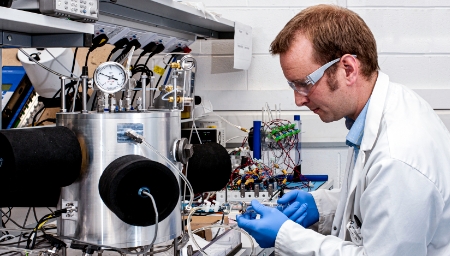
We set the bar high and measure success at each step of our product lifecycle whether it's design validation, supplier qualification, manufacturing measurements or customer satisfaction. Continuous improvement initiatives are data driven, using eight disciplines of problem solving (8D) and 5-Why methodologies. Our people, processes, and state-of-the art systems work together to ensure we deliver on our quality promise for customers around the world.